オーエスジー 渾身の新製品『GREEN TAP』のここが凄い! ~穴開け開発チーム 溝口さんに聞く~
省エネへの改善努力は経営戦略として欠かせない要素
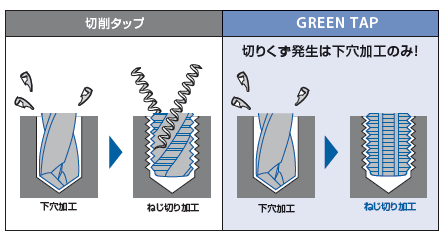
―製造業は循環型社会への実現に向けて関連性も深く、現在、省エネへの改善努力も注目されるようになりました。企業が戦略的にSDGsに取り組むことは持続的成長を促すことにつながり、新たな利益を生み出すとして、経営戦略としても欠かせない要素です。貴社のタップ生産時による具体的なCO2削減について教えてください。
溝口 M6を例にしますが、従来、タップ1本つくるには1.1KgのCO2を排出していました。このCO2排出量はタップ1本製造時に必要な消費電力量から算出〈注:CO2排出量=消費電力(kW)×時間(h)×CO2排出係数(kg-CO2/kWh)〉していますので、新製品であるGREEN TAPのCO2排出量が半分に削減できることは消費電力量が従来の半分に抑えられることと同じです。
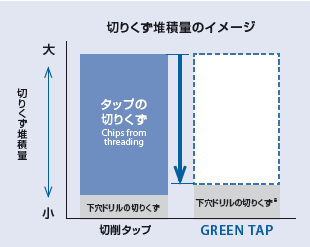
―なるほど。新製品を使用するお客様のメリットは。
溝口 こちらもCO2排出量の削減効果にぜひ注目していただきたいと思います。タップを1年で1,200本使用するお客様が従来品をGREEN TAPに置き換えると約660kgのCO2を削減することができます。これはガソリン車を電気自動車に替えて1年間に1万㎞ほど走った場合のCO2の削減量に匹敵します。また、盛上げタップは切りくずが排出されないため、切りくず除去のための機械停止時間を削減でき、タップの安定加工と長寿命化により、工作機械の消費電力量を抑えることができるのです。こうした理由から従来のタップをGREEN TAPに置き換えるだけでCO2の削減ができます。
古い技術と最新技術を掛け合わせてできた製造方法
―開発プロセスを改善した点はありますか。
溝口 今までは開発者のアイデアを紙の図面に描いて実際に工具の試作を行って加工試験を行っていました。このプロセスを何度も繰り返して良いものをつくり上げていくイメージです。一方、このGREEN TAPは、紙の図面からCADに置き換え設計することで、シミュレーションをもとに最適な形状を導くことができるので、何度も試作と加工試験を繰り返していた時間を省くことが可能になりました。そのおかげで開発期間を短縮でき、開発時のCO2排出量削減にも寄与することに繋がりました。
―既存のプロセスをデジタルに置き換えたのですか。
溝口 なにもかもゼロから生み出したわけではなく、既存の技術と最新技術を掛け合わせてできたものになります。イノベーションは、今まであった技術と新しいものの化学融合的なものになるので、GREEN TAPに込めた製造技術はまさしくイノベーションと呼べるでしょう。
―現在製造業でも労働減少の人口が問題視されていますから、蓄積された技術や技能を継承していくための手法も時代に合致したものでなくてはならないと感じます。
溝口 労働人口の減少や現場の高齢化により技術が失われていく危機感は弊社も直面しています。優れた技術をみすみす逃してしまうと、二度と手に入らないものになってしまうのでデジタルを駆使し、最新技術を用いて復活できないか、というところから開発は始まっています。今回は、熟練作業者の勘やコツで高品質なものをつくる作業を、最新の測定や3次元の設計、CAEなどの解析を用いて、今までの職人技をデジタル化することで、新たな技術として再生することができました。